Robotic Waterjet cutting is a revolutionary technology that combines the precision of waterjet cutting with the efficiency and flexibility of robotic automation. This cutting-edge innovation has gained traction across various industries due to its versatility, accuracy, and cost-effective nature. In this article, we will delve into the world of Robotic Waterjet cutting, exploring its benefits, applications, and future prospects.
Robotic Waterjet cutting is a process that utilizes a high-pressure jet of water, mixed with abrasive particles, to cut through a wide range of materials, including metal, glass, stone, composites, and more. The precision of the waterjet allows for intricate and complex cuts, while the robotic automation adds another layer of versatility and efficiency to the process.
One of the key advantages of Robotic Waterjet cutting is its ability to achieve high levels of accuracy. The robotic arm can be programmed to follow complex paths and patterns with micron-level precision, ensuring consistent and precise cuts. This level of accuracy makes Robotic Waterjet cutting ideal for applications where precision is critical, such as in aerospace, automotive, and electronics industries.
The flexibility of Robotic Waterjet cutting is another major benefit. The robotic arm can be programmed to cut through different materials, thicknesses, and shapes, making it highly adaptable to various cutting requirements. This flexibility allows for a wide range of applications, from simple straight cuts to complex 3D shapes, making it suitable for diverse industries and applications.
The efficiency of Robotic Waterjet cutting is also noteworthy. The robotic arm can work tirelessly without fatigue, leading to increased productivity and reduced labor costs. Moreover, the automated process minimizes material waste as the waterjet cuts with a narrow kerf, resulting in higher material utilization. This makes Robotic Waterjet cutting a cost-effective option in the long run.
The applications of Robotic Waterjet cutting are vast and varied. In the automotive industry, it is used for precision cutting of metal components, such as gears, chassis, and exhaust pipes. In the aerospace industry, it is used for cutting complex shapes in materials like titanium and composites, which are critical in manufacturing aircraft components. In the architecture and construction industry, it is used for precise cutting of stone, glass, and ceramic tiles for intricate designs. In the electronics industry, it is used for cutting printed circuit boards (PCBs) with high precision. These are just a few examples of the many industries where Robotic Waterjet cutting has found immense value.
The future prospects of Robotic Waterjet cutting are promising.
Advancements in robotics and automation technology are making Robotic Waterjet cutting even more precise, efficient, and versatile. With the integration of machine learning and artificial intelligence, the robotic arm can adapt to changing cutting conditions in real-time, leading to improved cutting performance and reduced downtime. Additionally, the use of sensors and cameras can enhance the accuracy and speed of the cutting process, making it even more reliable and efficient. The potential for further innovation and advancements in Robotic Waterjet cutting is vast, and it is expected to continue transforming industries in the coming years.
One of the notable trends in Robotic Waterjet cutting is the integration of collaborative robots, also known as cobots. Cobots are designed to work safely alongside humans, without the need for extensive safety barriers, making them ideal for small and medium-sized enterprises (SMEs) or workshops with limited space. Cobots can be programmed to perform various tasks in Robotic Waterjet cutting, such as material handling, part loading/unloading, and tool changing, further enhancing the automation and productivity of the process.
Another significant trend is the use of advanced CAD/CAM software in Robotic Waterjet cutting. CAD (Computer-Aided Design) software allows designers to create intricate and complex designs that can be translated into cutting paths for the robotic arm. CAM (Computer-Aided Manufacturing) software, on the other hand, optimizes the cutting paths, taking into consideration factors such as material properties, cutting speed, and efficiency. These advanced software tools enable manufacturers to maximize the potential of Robotic Waterjet cutting, creating highly customized and precise cuts that were once thought to be impossible.
The adoption of Robotic Waterjet cutting is also driven by the increasing demand for sustainability and environmental consciousness. Traditional cutting methods, such as laser cutting or plasma cutting, often generate harmful fumes, heat, and waste that can be detrimental to the environment and human health. In contrast, Robotic Waterjet cutting is a cold-cutting process that does not produce heat or hazardous fumes, making it an eco-friendly option. Additionally, the ability to cut with a narrow kerf minimizes material waste, reducing the environmental impact and promoting sustainable manufacturing practices.
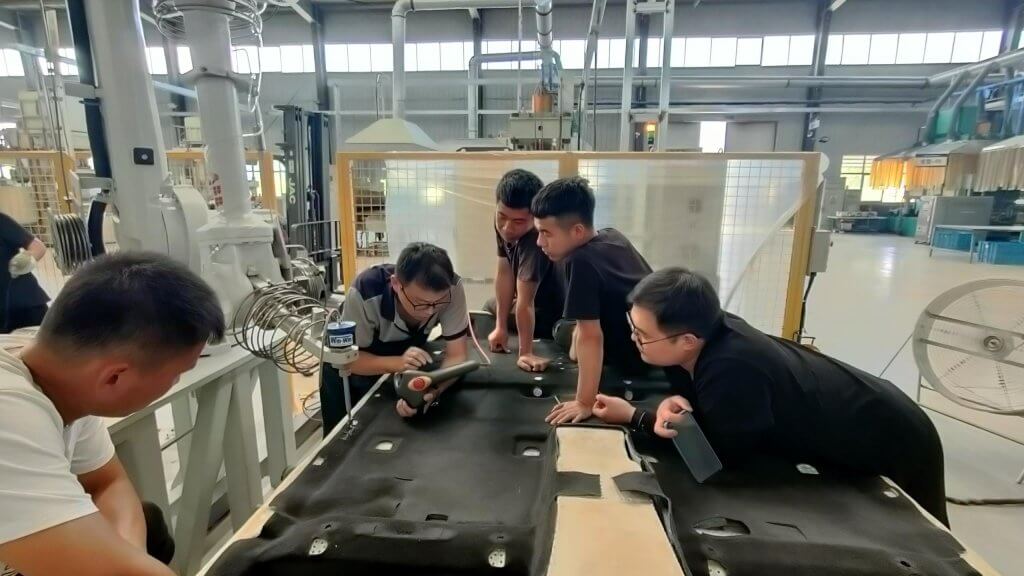
In recent years, Robotic Waterjet cutting has also witnessed advancements in the area of 3D cutting. Traditional waterjet cutting methods are limited to cutting in 2D planes, but with the integration of robotics, Robotic Waterjet cutting can now cut complex 3D shapes with ease. This has opened up new possibilities in industries such as aerospace, automotive, and architecture, where the demand for 3D components and structures is growing. The ability to cut 3D shapes with high precision and flexibility has further expanded the applications and versatility of Robotic Waterjet cutting.
Moreover, Robotic Waterjet cutting is also being used in the field of additive manufacturing or 3D printing. Additive manufacturing is a process where objects are created layer by layer using a digital design file. Robotic Waterjet cutting can be used to precisely trim and finish 3D printed parts, removing excess material, and refining the surface finish. This integration of Robotic Waterjet cutting with additive manufacturing has enabled the production of complex and high-quality parts with reduced post-processing requirements, saving time and costs.
Despite the numerous benefits and advancements, Robotic Waterjet cutting also comes with some challenges. One of the challenges is the initial investment cost. Implementing robotic automation requires a significant investment in robotic arms, sensors, software, and training. However, the long-term cost savings in terms of increased productivity, reduced labor costs, and material waste can outweigh the initial investment. Moreover, as the technology continues to advance, the costs are expected to decrease, making it more accessible to small and medium-sized enterprises (SMEs).
Another challenge is the need for skilled operators and programmers to operate and program the robotic arm. While the robotic arm can perform repetitive tasks with high precision, it still requires skilled operators to program and set up the cutting parameters, material handling, and tool changing. The shortage of skilled operators and programmers can be a limitation for some companies in adopting Robotic Waterjet cutting. However, as the technology progresses, user-friendly interfaces and intuitive programming software are being developed to simplify the programming process and reduce the dependency on skilled operators.
In terms of safety, Robotic Waterjet cutting requires strict adherence to safety protocols to protect operators and ensure safe operations. The high-pressure waterjet and abrasive particles can be hazardous if not handled properly. Proper training, safety barriers, and personal protective equipment (PPE) are essential to ensure safe operation. Collaborative robots (cobots) are being integrated to make the process even safer by working alongside humans and minimizing the risks associated with human-machine interaction.
In conclusion, Robotic Waterjet cutting is a cutting-edge technology that combines the precision of waterjet cutting with the efficiency and flexibility of robotic automation. Its benefits include high accuracy, flexibility, efficiency, and sustainability, making it a popular choice in various industries. The integration of robotics with waterjet cutting has revolutionized the manufacturing process, allowing for intricate and complex cuts with high precision, 3D cutting capabilities, and integration with additive manufacturing.
The versatility of Robotic Waterjet cutting is evident in its applications across various industries. In the aerospace industry, it is used for cutting complex shapes and contours in materials such as composites, titanium, and aluminum, enabling the production of lightweight components with tight tolerances. In the automotive industry, Robotic Waterjet cutting is used for trimming and shaping automotive parts, such as interiors, exteriors, and body panels, with high precision and speed. In the architecture and construction industry, it is used for cutting decorative elements, stone, glass, and ceramics, allowing for intricate and artistic designs. Robotic Waterjet cutting is also widely used in industries such as marine, electronics, energy, and healthcare, among others.
The benefits of Robotic Waterjet cutting are not limited to its accuracy and versatility. It also offers increased productivity and cost savings. With robotic automation, the cutting process can be performed 24/7 without the need for breaks or shifts, resulting in higher productivity and reduced labor costs. The ability to program and optimize cutting paths using advanced software tools also minimizes material waste, leading to cost savings and reduced environmental impact. The cold-cutting process of Robotic Waterjet cutting also eliminates the need for additional processing steps, such as heat treatment or deburring, saving time and costs in the overall manufacturing process.
Furthermore, Robotic Waterjet cutting also enhances workplace safety. The integration of safety features such as sensors, safety barriers, and collaborative robots (cobots) minimizes the risks associated with human-machine interaction. Operators can work in a safer environment, reducing the chances of accidents and injuries. The elimination of heat and fumes in the cutting process also improves air quality in the workplace, creating a healthier working environment for operators.
The future of Robotic Waterjet cutting looks promising with continuous advancements in technology. As robotics and automation continue to evolve, Robotic Waterjet cutting is expected to become even more precise, efficient, and user-friendly. Improved software tools, intuitive interfaces, and machine learning capabilities are expected to further streamline the programming and operation of robotic waterjet systems, reducing the dependency on skilled operators. Additionally, the integration of advanced sensors and artificial intelligence (AI) can enable real-time monitoring and feedback, allowing for adaptive cutting strategies and predictive maintenance, further optimizing the cutting process.
In conclusion, Robotic Waterjet cutting is a cutting-edge technology that combines the precision of waterjet cutting with the efficiency and flexibility of robotic automation. Its numerous benefits, including high accuracy, versatility, sustainability, increased productivity, and workplace safety, make it a compelling choice for various industries. With continuous advancements in technology, Robotic Waterjet cutting is poised to revolutionize the manufacturing process and pave the way for innovative and sustainable manufacturing practices. As the industry evolves, Robotic Waterjet cutting is expected to play a crucial role in shaping the future of manufacturing, offering new possibilities for customization, complexity, and efficiency in the production of a wide range of materials and products.
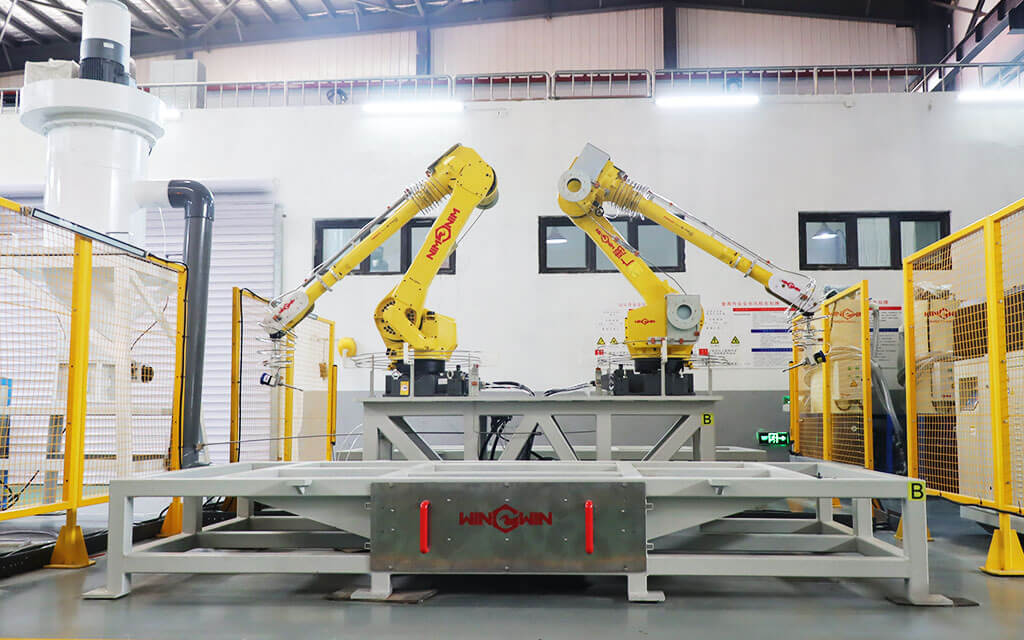
WIN-WIN robot waterjet cutting solutions
Win-Win Waterjet Co., Ltd is a leading manufacturer and provider of robotic waterjet solutions that have gained widespread recognition for their cutting-edge technology and innovative capabilities. With a strong commitment to quality, reliability, and customer satisfaction, Win-Win Waterjet Co., Ltd has established itself as a trusted partner in the field of robotic waterjet cutting.
One of the key offerings of Win-Win Waterjet Co., Ltd is their state-of-the-art robotic waterjet system. This cutting-edge solution combines the precision of waterjet cutting with the efficiency and flexibility of robotic automation, delivering superior results in various industrial applications. The robotic waterjet system offered by Win-Win Waterjet Co., Ltd is known for its high accuracy, versatility, and advanced features that optimize the cutting process.
The robotic waterjet solution by Win-Win Waterjet Co., Ltd is designed to handle a wide range of materials, including metals, composites, glass, ceramics, and more. With 3D cutting capabilities, it enables the production of complex shapes and contours with high precision, allowing for intricate and detailed cuts. The system is equipped with advanced software tools that enable programming and optimization of cutting paths, minimizing material waste and maximizing productivity. The intuitive interface and user-friendly controls make it easy to operate, reducing the dependency on skilled operators.
One of the standout features of Win-Win Waterjet Co., Ltd’s robotic waterjet solution is its focus on sustainability. The cold-cutting process eliminates the need for additional processing steps, such as heat treatment or deburring, reducing the overall environmental impact. The system is also designed to be energy-efficient, minimizing energy consumption during operation. Furthermore, the integration of sensors and artificial intelligence (AI) allows for real-time monitoring and feedback, enabling adaptive cutting strategies and predictive maintenance, optimizing the cutting process for maximum efficiency.
Win-Win Waterjet Co., Ltd also places a strong emphasis on workplace safety. The robotic waterjet system is equipped with advanced safety features, including sensors, safety barriers, and collaborative robots (cobots), ensuring safe human-machine interaction. Operators can work in a secure environment, reducing the risks of accidents and injuries.
In summary, Win-Win Waterjet Co., Ltd offers a cutting-edge robotic waterjet solution that combines the precision of waterjet cutting with the efficiency and flexibility of robotic automation. With its advanced features, sustainability focus, and commitment to workplace safety, the robotic waterjet solution by Win-Win Waterjet Co., Ltd is a top choice for various industrial applications, delivering superior results and driving innovation in the field of manufacturing.